大岩山銅鐸の復元
銅鐸博物館では展示作品の製作と古代の鋳造技術の再現実験を目的に、弥生時代の技法に近い
やり方で大岩山銅鐸の復元実験を行っています。
銅鐸の作り方
鋳造(ちゅうぞう)とは
所要の形状に作られた型(鋳型)に高温度に加熱、溶融し流動状となった金属(湯と呼ぶ)を注入したのち固まらせて、鋳物(いもの)を作る作業を鋳造(ちゅうぞう)と言います。銅鐸の場合、銅鐸の形をした空隙を持つ型を「銅鐸の鋳型」と呼びます。銅鐸のような中空のものは、外側の形を持つ「外型」と内側の形を持つ「中型」またま「中子(なかご)」が必要です。外型と中子の隙間に溶けた青銅を流し込み、冷却して取り出すと銅鐸の出来上がりです。
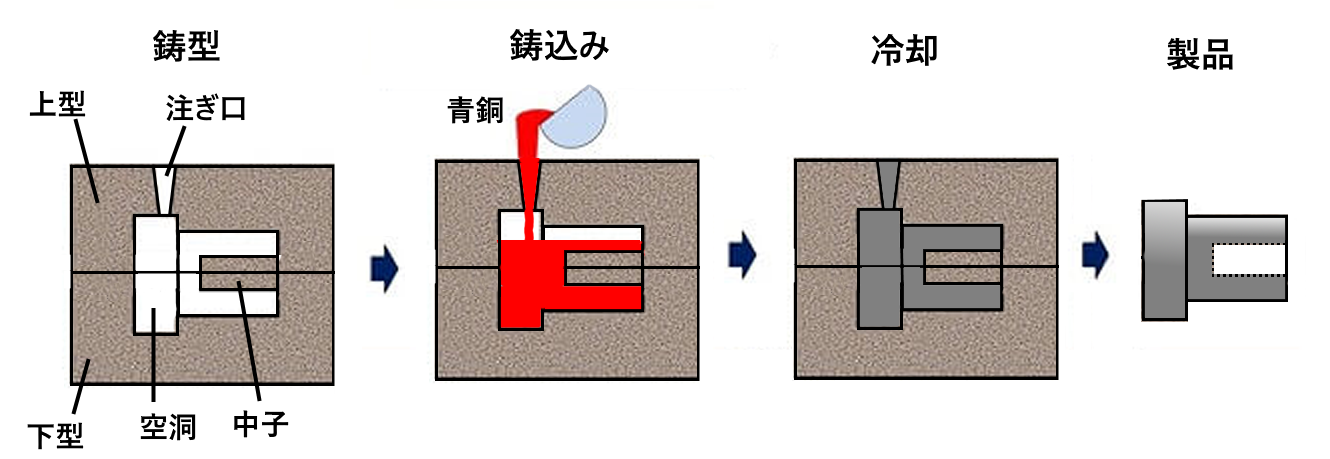
鋳造による鋳物製品の製造工程 [イラスト 田口一宏]
鋳型作りと鋳造
【真土(まね)型鋳造とは】
鋳型を作るやり方は、現在ではいろいろな方法がありますが、弥生時代は、小さな古い銅鐸は石製の鋳型を、大きく新しい銅鐸は土製の鋳型を用いていました。石製鋳型は、現在なら金属型に相当し、土製鋳型は、現在でもポピュラーな「砂を用いて鋳型を作る砂型鋳造法」に当たります。弥生時代の鋳造でも、砂型鋳造法使われていたということです。現在は、鋳造用の特殊な砂を用いますが、当時は粘土を使っていました。
粘土と言っても、真土(まね)と言って、ち密で耐熱性のある粘土を使います。これは、粘土と川砂を混ぜ一度焼いた後、細かく砕き、篩(ふるい)にかけて作ります。非常にキメの細かい真土から粗い真土まで数種類の真土を使い分けています。
我が国において、工芸品、銅像などの製作に際し、古来より伝統的に用いられてきた方法です。
銅鐸博物館で復元製作するとき、弥生時代のやり方を踏襲して作ろうということで真土型鋳造を採用したようです。
【土製鋳型の製作】
土製鋳型の作り方もバリエーションがあるのですが、一つの方法を示します。真土は粘土汁で練り、藁などを混ぜて使います。藁を混ぜることにより強度が上がるのと、焼いた時に微細な隙間が出来て、鋳造時に発生するガスを逃がす効果があります。鋳造後、型を壊して製品を取り出すのですが、多孔質になっているため、壊しやすいというメリットもあるそうです。
図では、真土は1層として描いていますが、実際には、粗い粗真土や中真土、仕上げ真土、粉真土など数層から成っています。
![]() 1.粘土で台座作り |
![]() 2.真土で外形造り |
![]() 3.外形と紋様の彫り込み |
![]() 4.外形を使って中子作り作り |
![]() 5.中子の彫り込みり |
![]() 6.外形を中子の合体 |
銅鐸鋳型の製作工程 (イラスト:田口一宏)
この図には、乾燥や素焼き、仕上げなどの工程は示していません。
【鋳造】
この型に溶けた青銅を流し込んで銅鐸を作ります。弥生時代、溶けた青銅は溶融炉から「とりべ(高坏型の土器)」に取り出し、鋳型に流し込んでいました。
![]() 7.青銅の流し込み |
![]() 8.鋳型を開く(大岩山銅鐸復元実験) [写真:野洲市歴史民俗博物館] |
銅鐸博物館での復元実験
銅鐸博物館では、銅鐸の復元実験を2回行っています。
1回目は、昭和63年(1988)、銅鐸博物館の開館にあたり、39cm高さの昭和4号銅鐸の復元で、2回目は、開館10周年の特別展に展示用に135cmの最大銅鐸(明治1号鐸)の復元実験です。
作り方は、できるだけ弥生時代に使われたと考えられる鋳造方法を使っています。基本的には上の図の通りですが、るつぼなどの道具や溶融炉や送風機などの付属設備、耐熱用具などは現在のものが使われました。
なお、2度にわたる鋳造実験は小泉武寛氏と青銅器工房和銅寛の方々が関わりました。
第1回復元実験(昭和4号銅鐸 39cm高)
詳細は野洲町立民族資料館研究紀要 創刊号(1989)に記載されています。復元実験は昭和63年に実施されました。対象としたのは、昭和4号銅鐸 高さ:39cm、裾幅:25cm×31cm です。鋳造に当たって最も強く意識したのは、厚さ2〜2.5mmという薄さだそうです。実物の厚さのデータは分かりませんが、一般にこのくらいの大きさの銅鐸は、厚みが2mmと言われており、鋳造技術者の間では驚嘆の目でもって語られています。最新技術を使ってもようやくできるかどうかというレベルの高さで、当時の技法で作るとなると、ただただ驚きなのだそうです。
今回の鋳造実験では2.5mmを設計値としていました。
もう一つ、銅鐸の紋様を忠実に再現することにも力点を置いたようです。
詳しい条件は除きますが、製作の過程は次の通りです。
【粘土で台座作り】
粘土を積み上げて外型の台座を作る。出来上がった台座を十分乾燥させ、次いで素焼きをする。(所感:弥生時代の土型の詳細が分かってないのですが、真土を載せる粘土の台座を作るのは一般的だったのか? 唐古鍵遺跡からは素焼きの台座が出ているようだが、素焼きすると硬くなって後世に数多く残るような気がします。)
【真土で外型作り】
素焼きの台座に、粗い真土を塗りその上にキメの細かい仕上げ用真土を塗り重ねる。ここで重要なのは、銅鐸の身のきれいなカーブの出し方です。今回の鋳造実験では、Y字形の木の枝2本を使ってここに長い木の枝を渡して軸木とする。この軸木に竹のへらを結び付けて、軸木を回転させて、まだ柔らかい真土を掻きとるときれいな身のカーブが描けます。
弥生時代の工人もこのような工夫をしていたのでしょう。
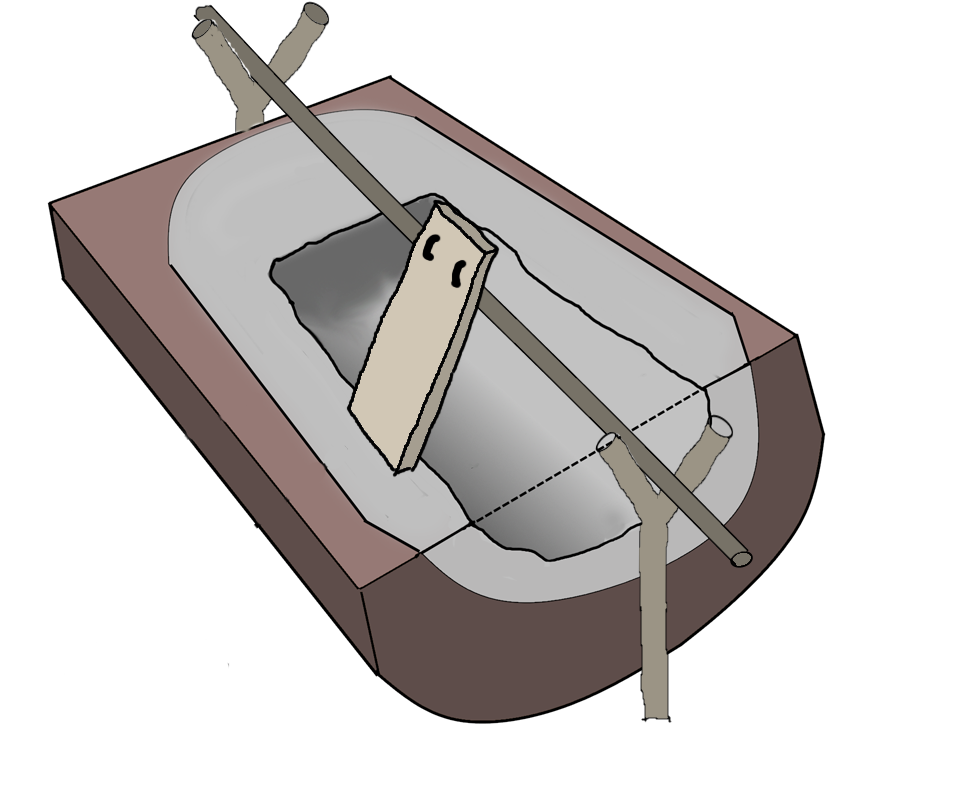
銅鐸のカーブの出し方(治具) [イラスト 田口一宏]
【銅鐸の形状と紋様の彫り込み】
真土が乾いてから、銅鐸の鈕と鰭になる部分を削り取る。次いで、鈕・鰭・身の紋様を竹へらで削り込んでいく。
このような作業を2個の外型に施す。
緻密で時間のかかる作業で、片面で5日間かかったそうです。
【真土の肌焼】
模様を彫り込んだ外型を焼しめるために肌焼を行う。 この鋳造実験では、簡単な炉を作り、外型をうつ伏せにして炭火で焼く。この時、真土の表面にはススが付くが、鋳造後の離型剤の役を果たす。【中子作り】
2個の外型を合わせてひもで結び、鈕になる部分を下にして立てる。筒状になった中空の底(舞に相当)と内側に、山砂に粘土汁を混ぜたものを塗っていく。その上から粗真土を上塗りし補強していく。このようにして中空の中子が出来る。
【中子の彫り込み】
乾燥してから中子を取り出し、銅鐸の厚み分となる2.5mmを均一に削り取る。このとき、型持孔となる部分は残しておく。
内面突帯となる線を彫り込む。溶けた青銅を流し込む湯道や空気の出口となる湯上り口も同時に削り込んでおく。
削り込んだ内面は砂でザラザラしているのでキメの細かい真土を塗り込んでおく。
その後、よく乾かしてから重油窯で素焼きを行う。
(所感:弥生時代、中子を作った後に素焼きしていたのか? 気になります。)
【外型と中子の型合わせ】
外型と中子を組合わせ、全体を粗い真土で塗り込み、一体ものの鋳型とする。【型焼き】
出来上がった鋳型に青銅を流し込む前に、型を焼いて温度を上げておく。弥生時代には野焼きをしていたと思えるが、今回はレンガで簡単な窯を作って、炭で焼いた。
【青銅の溶解と鋳込み】
型焼に並行して材料(銅、錫、鉛)合計で18Kgの溶解を開始。この時、湯(溶けた青銅)の脱酸剤となり、また、湯の流れを良くすると言われるリンを添加した。青銅を溶かす坩堝(るつぼ)は黒鉛製のものを使用し、燃料にはコークスを使い、電気モータで送風した。 鋳型の温度も上がり、青銅の溶解もできたら、炉より坩堝を取り出し、鋳型の湯口より流し込む。【割り出し・仕上げ】
温度が下がってから、外型と中子をくるんでいる粗真土を砕き、鋳型を取り出す。次いで、外型を開いて出来上がった銅鐸を取り出す。
バリや銅鐸の表面に付着している真土を取り除き、銅鐸面を磨いて仕上げる。
【鋳造結果】
鋳型を2個作り、2回の鋳造を行った結果、細かい欠損を除き銅鐸を作ることが出来た。1つ目の鋳型での鋳造は、2つの外型の位置ずれが生じバリや欠損が生じた。ビデオ収録のため何回も組み合わせを行ったり、型焼の時間が長かったりしたのが原因かもしれない。
外型や中子に補強材を入れなくても型崩れを起こすことはなかった。
炉や坩堝など弥生時代にはなかった設備を使ったが、弥生時代に使われたと考えられる鋳型の作り方で銅鐸を作ることができた。
第2回復元実験(明治1号銅鐸 135cm高)
詳細は野洲町立民族資料館研究紀要 第8号(2001)に記載されています。対象としたのは、明治1号銅鐸 高さ:135cm、裾幅:49cm×43cm です。
鋳造する銅鐸は厚さ3.5mmという設計です。実物の厚さは記載されていませんが、3mmと言われています。銅鐸博物館の開館10周年記念の事業として、大岩山で見つかった日本最大の銅鐸の復元を目指して1998年(平成10年)に実施されました。
第1回目の約40cm高さの銅鐸に比べ、はるかに大きく鋳型がうまく作れるか、溶けた青銅がうまく鋳型の中を流れるか、多くの課題を抱えた鋳造実験でした。
作り方は1回目の銅鐸とはいくつか違う点があり、比較しながら補足説明をします。 今回のやり方を見ていると、弥生時代はどうしていたのだろうといろいろな疑問が出てきます そのようなことも、補足して述べます。
【外型作り】
![]() 銅鐸鋳造用の原型 [写真:野洲市歴史民俗博物] |
対応策として、アクリル板と石膏で概略の原型を作り、これを基に外型を作ることとした。
この原形の片側の上に真土を覆い、その上に粗い真土、また上にさらに粗い真土を積み重ね、外型を作るが、途中の層中に取扱い用や運搬用に鉄筋を組み込んだ。
[補足]原型を使う方法は、現在では普通であるが、弥生時代にはなかったのでは?
原型を使うこと、このため粘土を素焼きした台座は不要なので作らなかったこと、などが1回目の鋳造実験とは異なる。
鉄筋を外型に組み込むのも1回目とはことなる。ただ、外型の大きさや重量を考えると、弥生時代にも、硬い木の枝などを木筋として組込んだのかもしれない。そうだとしても、鋳造後は、外型は破壊されるし、高温にさらされた木筋は崩れて後に残らないだろう。
次に反対面の外型を同様に作る。
出来上がった2個1組の外型の内面を炭火で軽く焼く。
【中子作り】
外型を仰向けに置き、紙に油を引いて敷き、その上に厚さ3.5mmの粘土を貼り付ける。これが銅鐸の厚みとなる。ただし、型持孔になる部分には粘土を貼らない。粘土の上に砂の多い真土を置き、その上に鉄筋を組み、さらに真土を置いて乾燥させる。
真土の上に炭を置いて軽く焼くと、外型の上に中子の半切のものが出来上がる。
中子を外型から外し、厚み分の粘土をはぎ取ると半切中子が出来上がる。これを2個貼り合わせることにより、中子が暫定的に完成する。
型持孔は粘土を貼るときから作り込まれているので、内面突帯を彫り込む。湯道や湯上り口も同時に削り込んでおく。この後、表面を炭火で焼いておく。
[補足]1回目の実験では、外型の上に直接中子用の真土を置いて中子を作り、後から中子を削り取って、銅鐸の厚みとしたが、今回は銅鐸の厚み分の粘土を貼りつけ、後から粘土を剥がせば厚み分の空隙が取れることになる。
このやり方は、1回目の実験とは異なるが、現在の美術工芸品などで、使われているようだ。
出来上がった中子の形状からはどちらの方法で作ったか分からないと思われる。
弥生時代、銅鐸の厚みはどのようにして制御していたのだろうか?
今回の試作では、外型と中子双方に鉄筋が入っており、これを使って固定したりウインチで釣り上げたりしているが、弥生時代にはこのような重量物をどのようにハンドリングしていたのだろうか?
上にも書いたが、補強用やハンドリング用に木筋を使っていたのだろうか? 木筋を入れて外周を木材で囲っておけば重い鋳型の扱いも楽になる、と弥生人も考えたのでは???
【紋様の彫り込み】
外型の表面に紋様を彫り込む。【型合わせ】
完成した外型、中子を組合わせる。それらを真土で塗り込んで一体ものとする。【青銅の溶解と鋳込み】
一体化した鋳型を重油窯で焼く。これに並行して材料(銅、錫、鉛)合計で約150kgの溶解を開始。2個のとりべ(取瓶:溶けた青銅を入れて運ぶもの)に取り、2つの湯口より一気に注ぎ込む。
[補足]弥生時代、高坏型土器をとりべとして使っていたが、何回にも分けて運ばざるを 得ない。時間の経過で温度変化が生じて鋳造に悪い影響を与えなかったのだろうか?
また、高熱対策はどうしていたのだろう?
【割り出し・仕上げ】
![]() 復元した銅鐸(明治1号銅鐸) [写真:野洲市歴史民俗博物] |
鋳型に塗り重ねた真土を砕き、外型を外し、銅鐸を取りだした。
型ずれから、片面に湯が回らず欠損した部分があった。もう片面は問題なく仕上がった。
前回と同様、銅鐸の鰭部分への真土の付着が著しいのと接合部分のバリが生じていた。
欠損部分は、鋳掛け(いかけ)と言う手法で解けた青銅を部分的に注いで補修した。
バリを鏨(たがね)で切ったり、削り取って磨きをかければ完成。
【鋳造結果】
おおよそ3.5mmの厚さで鋳造し、製品の重量は約55kgとなった。実物は約45kgである。実物の厚みは約3mmという報告があり、厚みの差が重量差になったことが判る。
今回試作した方も「古代の工人の素晴らしさに感心させられた」と結んでいる。
第2回復元実験(明治1号銅鐸)の予備実験
銅鐸博物館では、古代の方法に近いと考えられる復元実験に先立ち現在の鋳造技術で明治1号銅鐸の復元予備実験を行っています。大阪の弥生文化博物館の開館展示のために大岩山の明治1同銅鐸の複製を製作していました。
この時の石膏鋳型が残されており、銅鐸博物館では、この鋳型を使い中子は新作して鋳込み実験をしています。この時は、ガス型法という現在の技術を使い鋳造しています。
この実験ではうまく銅鐸が出来ていますが、重さは60Kgと第2回目の復元実験より重くなっています。
このことからも、古代の鋳造技術の素晴らしさが判ると共に、この大きさでの3mm厚みの難しさが分かります。